Here's the third installment of this series. I am so fascinated by this material that I didn't have a word limit for the other two posts. I'm sorry to those who're saturated with bamboo but I didnt want to leave any strings loose in the air, so to speak.

In this post, Nick replies to them so we can get an idea of what his ideas are and where he's going to go with them. For me, it was a good learning process and I was quite appreciative of the fact that he spent some time out of his training and school to detail the building process with me.
A quick recap : Nick Frey is a mechanical engineering junior at Princeton University. He's also Espoir National Time Trial champion. He and friends teamed up to build a practical wooden road racing bike for a design project at school. They went from one to two and now three bicycles, at each step rectifying mistakes and learning more about the material and the process. Perfecting the art has been their goal throughout. Most importantly, their idea has culminated in a venture to start a company specializing in bamboo bicycles.
Chat With Nick Frey Continued...
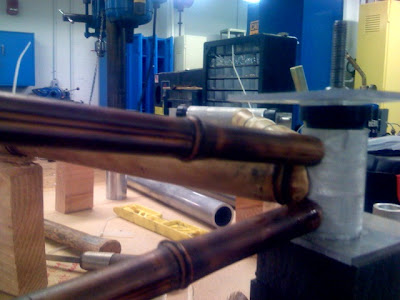
Nick : It was our design project for MAE 321: Engineering Design. Our inspiration was Calfee, but the idea for the company basically evolved from our love of thinking about and building these bikes and the fact that Calfee's are so overpriced and no one else makes them.
Me : The propane torching for the bamboo is totally new? I mean, are you looking to patent it? That'd be cool. Whats cutting tools do you use for bamboo (just saws?) and are you also employing any jigs for torching, assembly etc?

Me : Who supplied you with the oven and bamboo raw material for the pilot project?
Nick : We cut down our own because the stuff we were getting from Brazil was taking forever. We have actually realized that local stuff is the best! It has the right diameter, and there is a TON of variety for wall-thickness, nodal density, shape, etc. Also, we can cut it and treat it immediately, a key to preventing splitting and making it strong.
Me : What about an average time you've found to make Model Zero? Thoughts related to shortening the production cycle will depend on better technology (jogs and machinery), automated processes, simpler designs etc. (Big issue when you're running a company!)
Nick : Model Zero took a LONG time, but our third model is taking far less time (most of it was making the jig and creating/CNC'ing the dropouts). The time needed for cutting and treating the bamboo is about 1.5 hours, bake overnight, then mitering a whole bike takes another 1.5 hours to get it perfect, then making

Me : So who's putting down the initial investments? Contributions from a summer pizza job, or just friends chipping in ? ;)
Nick : He is getting an operation setup in Nigeria (born there, works closely with the national university there) and we should be making bikes by the summer! The cool part about this operation is the low investment in capital costs. The CNC'ing is outsourced easily, and then all we need is a small mill and lathe, and a Dremel, and we are golden. At this point, advertising and getting a shop in Boulder, CO to use as a nice showroom will be the majority of our cost, and that will not occur until after graduation when we have hopefully built a name for ourselves.
Me : Lastly, how do you ensure straightness in your tubes? Bamboo is all natural. Model Zero's down tube has a little angle 1/4th of the way from head tube (at least looks to me). I suppose you'll selectively pick your tubing then ?

* * *
Thank you for reading. I wish Nick and team the best of luck. I'm sure its a challenge juggling school with competition and now frame building. But I like to call problems challenges, they're never problems!
I'm sure you must have been following up on the North American Hand Made Bicycle Show. For those who haven't, be sure to check out the Cyclelicious Bicycle Blog for some good reports.
Bike Radar has some closeups of some of the bicycles. Also check out the Bike Forest Blog for awards news.
Here's a sweet picture from Cyclelicious, if its not straying too much away from our wooden bike theme.

I have seen bamboo bikes around before. They are interesting to me because they are a natural material. It will be interesting to see how successful these guys are.
ReplyDeleteChris,
ReplyDeleteIf you get your hands on one, feel free to share your experience.
wow,that's fantastic !!
ReplyDeleteYou guys are so cool@
it seems that the "overpriced" Calfee at $3000 is exactly the same price as Nick has chosen to sell his road frames...
ReplyDeleteTry to rate Lignin% in Bamboo, then contact “Dr. Cheu-Ching FOUN” for further discussing Bamboo mechanical force.
ReplyDeleteThe address for Dr. Cheu-Ching Foun is 4F, No. 26, Lane 39, Shuei Yuan Street, Yungho, Taipei, Taiwan
The mechanical function of Lignin in Coconut husk vs. Wood (Bamboo Lignin?)has been released to two female students before the begining of 2010 at the front of Department of Forestry and Resources Conservation, NTU.
Cheu-Ching FOUN, a member of www.acs.org
Taipei time: 4:17 Am, Tue., 1/27/2010